Common Functions of Industrial Control Screens
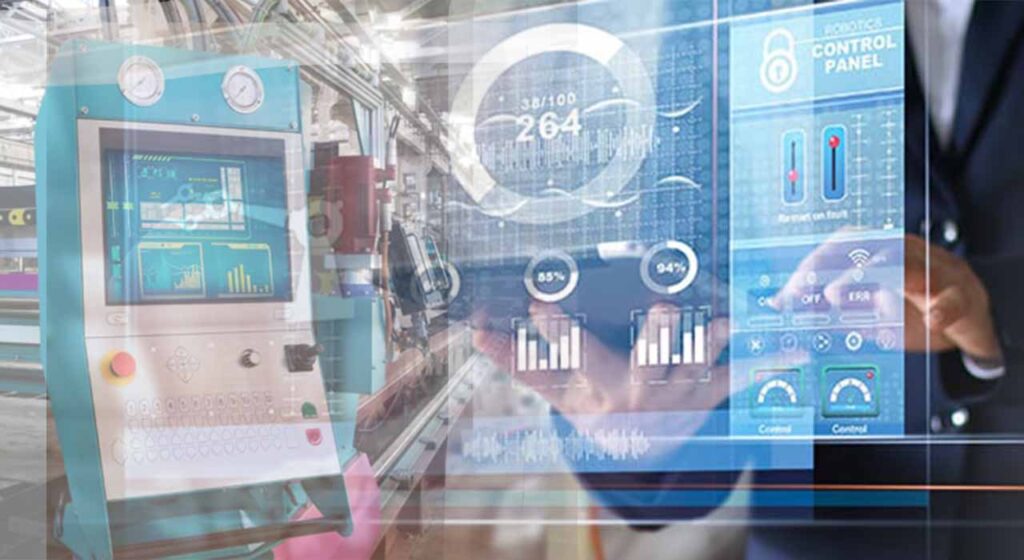
An advanced industrial control screen showing a user-friendly graphical interface.
Industrial control screens, also known as industrial monitors or touch panels, are critical human-machine interfaces (HMI) in industrial automation systems. These screens allow operators to monitor and control machines, production lines, and even entire factories intuitively. Modern industrial control screens integrate advanced computing capabilities, diverse interfaces, and powerful display and touch features, making them key components of smart manufacturing and Industry 4.0.
Key Features of Industrial Control Screens
1. Touch Operation
Modern industrial control screens are often equipped with resistive or capacitive touch panels. These enable users to control machines and processes with simple touch gestures, significantly enhancing convenience and efficiency.
Operators using a capacitive touchscreen to control production processes.
2. Real-Time Data Display
Industrial screens provide real-time data from sensors and control systems, such as temperature, pressure, speed, and flow rates. This enables operators to stay updated on equipment status and production processes.
3. Graphical User Interface (GUI)
The GUI on industrial screens allows users to interact using icons, menus, and graphics. This intuitive approach makes operations more user-friendly and easier to understand.
4. Trend Analysis
Many industrial screens display historical trend graphs, which are crucial for analyzing changes in production processes and optimizing operations.
A data trend graph showcasing production metrics over time.
5. Alarm Notifications
When anomalies or equipment failures occur during industrial processes, the screen provides alarm notifications, ensuring operators can respond promptly.
6. Recipe Management
In production processes requiring material mixing or formulations, industrial screens manage and adjust recipes, ensuring consistent product quality.
7. Remote Control and Monitoring
With advancements in network technology, industrial control screens enable remote monitoring and operation, improving system flexibility and convenience.
8. Multi-Language Support
To meet global demands, industrial screens typically support multiple languages, ensuring accessibility for users from different countries.
A multi-language interface simplifying operations for global teams.
9. Log Recording
Industrial screens can record operation logs and production data, which are invaluable for tracking production history, quality control, and maintenance.
10. Network Communication
These screens come with communication interfaces such as Ethernet, RS-232/485, and CAN, facilitating data exchange with PLCs, DCS systems, PCs, and other industrial devices.
11. Multi-Screen Interconnectivity
In complex industrial setups, industrial screens can connect to other screens for multi-point control and monitoring.
12. User Permission Management
For security, user permission settings ensure that only authorized personnel can perform specific operations.
User authentication settings on an industrial screen.
13. Durable Design
Industrial screens are designed to withstand harsh environments with features such as dustproofing, waterproofing, and shock resistance. They also operate reliably across a wide temperature range.
The Evolving Role of Industrial Control Screens
Industrial control screens are no longer just display devices—they are the core of data acquisition, process control, and human-machine interaction. As industrial automation and smart manufacturing evolve, these screens will play an increasingly important role, with their functions continuously expanding and improving.
Call to Action
Looking for reliable industrial control screens to elevate your automation systems? Explore our range of advanced displays or contact us today for a consultation!